About
Family business and Europe’s leading private processor
A family history
The Depestele group is a family business that has been involved in linen processing since 1850.
Europe’s leading private flax producer, with 3 production sites in Normandy, the Depestele Group is involved in everything from flax cultivation to scutching and combing.
The group collects flax from all over Normandy, as well as from the Île-de-France and Brittany regions, in collaboration with over 900 farmers .
Since 2009, Depestele has structured its R&D department to promote the use of flax products and co-products in composite materials. The group then set up a technical linen production center for the manufacture of reinforcements.
Since 2019, the Depestele Group has been ISO9001 certified for the design, development and production of technical semi-finished products from flax fibers.
Committed to the environmental and energy transition, the Depestele Group has joined BPI’s Coq Vert community.
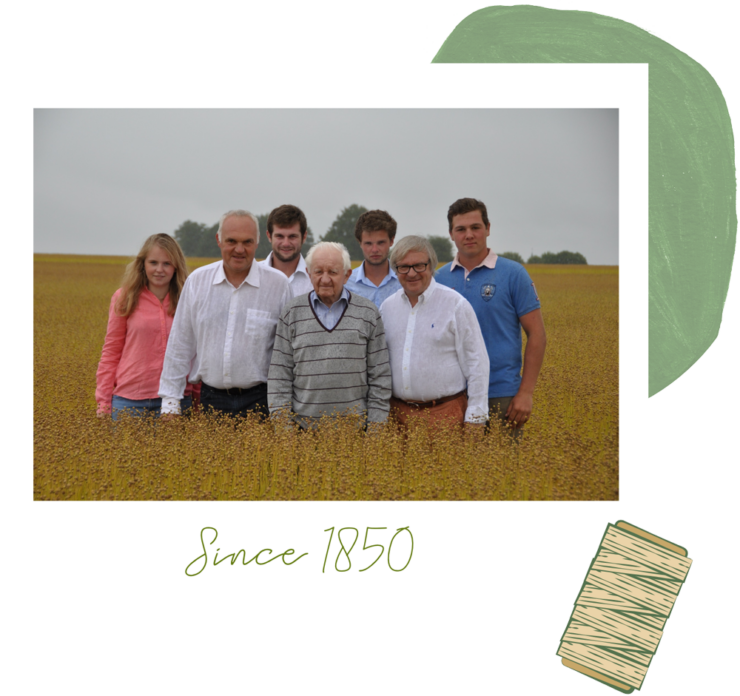
The Depestele group is :
>10%
of flax production in France
900
farmers
175
employees
80 000
tonnes of flax processed per year
6
scutching lines
2
combing lines
5
certifications
Our locations
Teillage Vandecadelaere & Linafil (Bourguébus, 14)
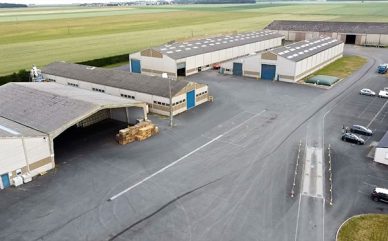
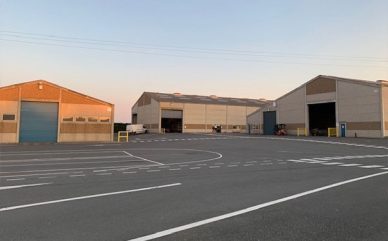
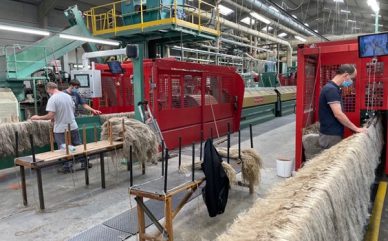
Linière de Bosc-Nouvel (Valmartin, 76)
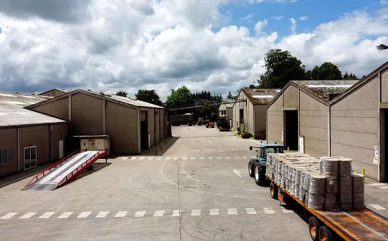
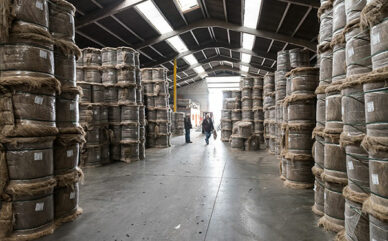
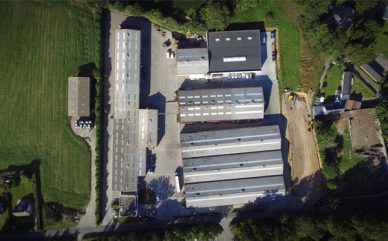
Teillage du Vexin (Saussay-la-Campagne, 27)
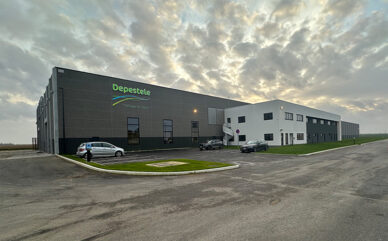
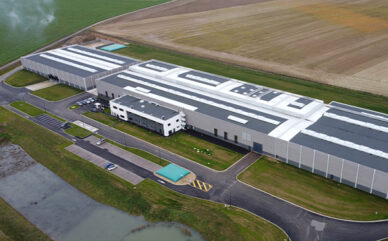
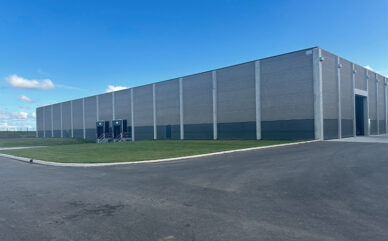
Our fields
In Normandy, at the heart of Europe’s best terroir, Depestele group passionately combines the verbs harvest, transform and enhance.
Since 1949, our priority has been to offer you the very best flax. Combining tradition and modernity, gathering human know-how and technology, we can help you conquer new markets.
Linen production stages
Sowing seeds between March and April. Flax plants mature after 100 days.
Flax plants are removed in mid-July and laid flat in the fields.
Retting is a crucial step for flax fibers. The straw is then harvested and baled.
The aim of scutching is to separate the various constituents of the flax stalks.
The flax is then prepared to be spun, the fibers will be divided in order to homogenize them.
The combed linen fibers are then blended to form ribbons: rovings.
Harvest:
A symbol of purity for over 10,000 years, flax is conquering new territories every day. A noble and eco-responsible material by excellence, flax deserves the most attentive care. Throughout the growing and harvesting phases, our technicians ensure regular monitoring of the plots and provide flax growers with all their knowledge to always obtain the best fiber possible. Every year, through our partnership of over 900 growers, we process more than 16,000 acres of flax.
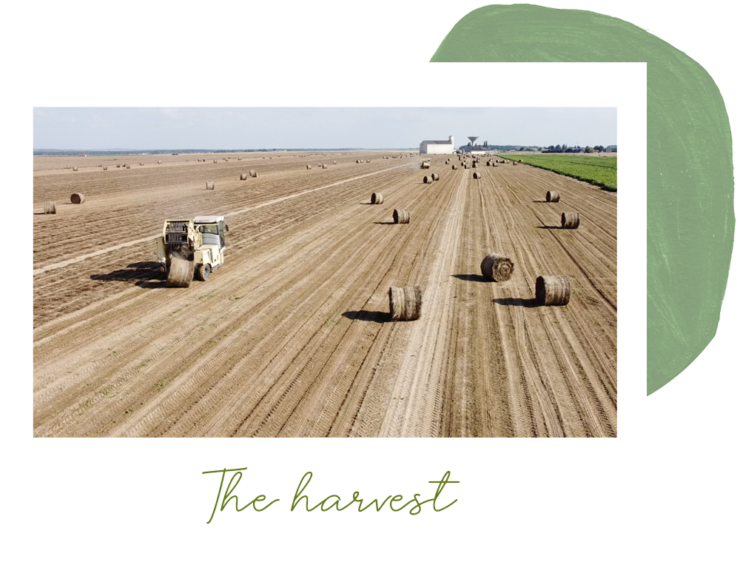
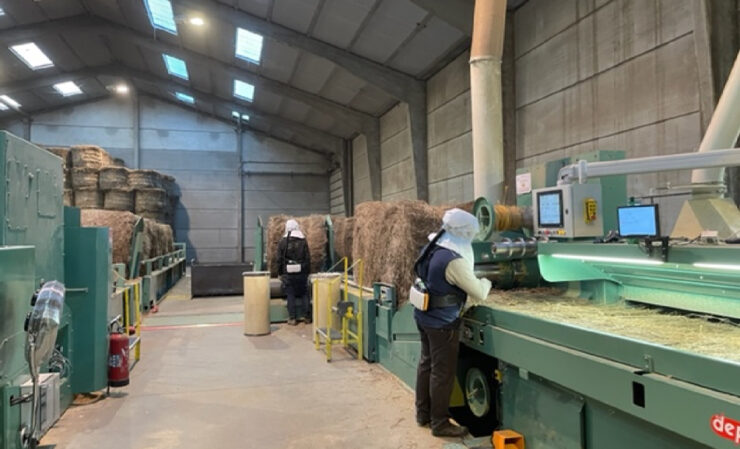
Transform:
Depestele is Europe’s leading private flax processor, working nearly 80,000 tonnes of flax straw each year.
Our 3 state-of-the-art industrial facilities enable us to offer you stable, consistent production quality, tailored to your specific needs. Our 3 cutting-edge industrial tools enable us to provide you with high-quality, stable and homogeneous production, tailored to your specific requirements.
Enhance:
Concerned with our producers freedom, we offer a variety of contracts and marketing methods to meet all the needs of our customers.
Depestele Group has direct commercial relations with spinning mills all over the world, seeking maximum added value for each product. Present at major national and international trade fairs, we keep a close eye on market trends, particularly in terms of diversifying outlets. Depestele has attracted customers in all sectors of activity and all over the world (95% of sales are exported).
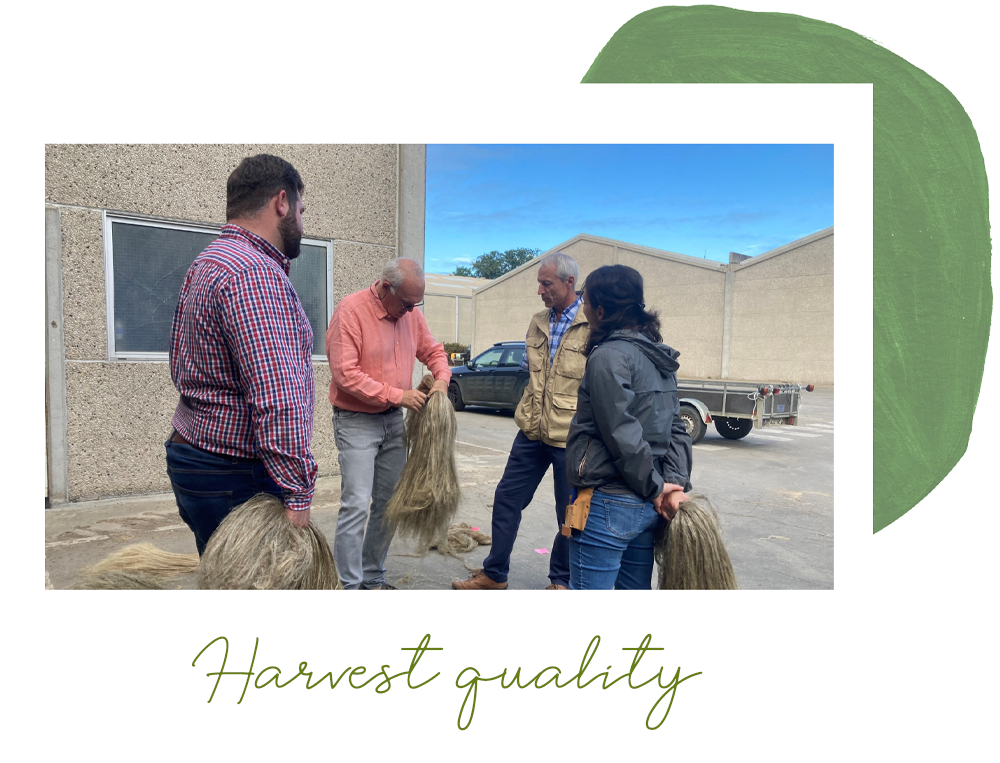
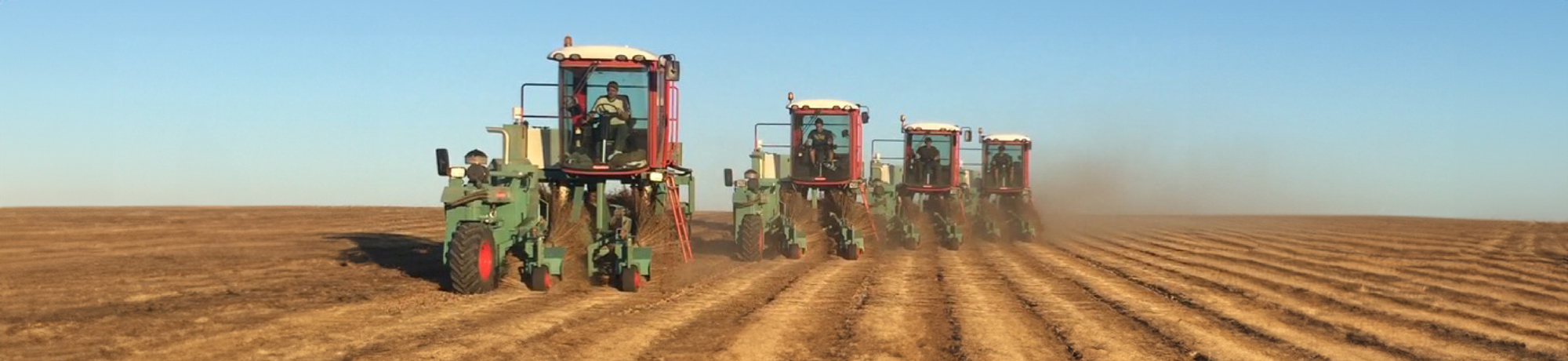
Research & Development
Over the past 15 years, the company has structured this department for the valorisation of long flax fibers in composite materials.
Creation of a CPLT (technical linen production center) for the manufacture of reinforcements in Bourguébus 14.
FLAXLAB: Depestele has joined forces with ENSICAEN CNRS to form a joint laboratory funded by the French National Research Agency.
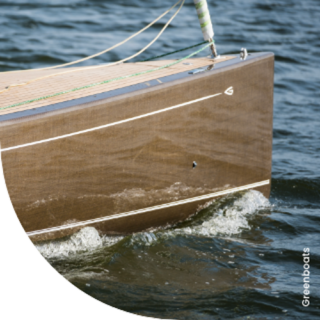
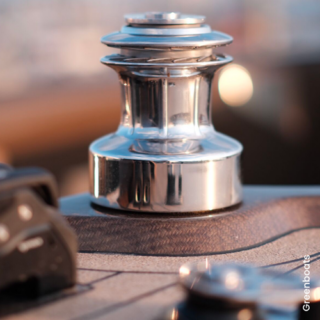
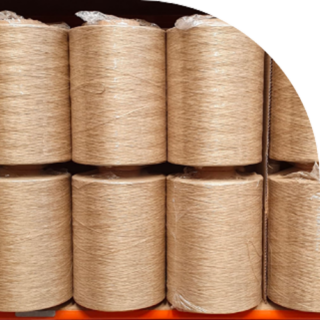
Depestele recovers around 80,000 tonnes of straw a year by extracting and marketing various products: long and short fibers (30,000 tonnes), shives (45,000 tonnes) and seeds (5,000 tonnes).
An integrated industrial processing unit enables the company to produce high-performance flax rovings using “engineered technical fibers”, grown under dedicated cultivation and developed specifically for the composites market.” The range contains rovings from 300 to 2400 tex, made in accordance with specifications that guarantee stable and controlled properties over time.
Key figures:
15 years
research & innovation
14
associated laboratories
4
doctors engineers
20
department employees